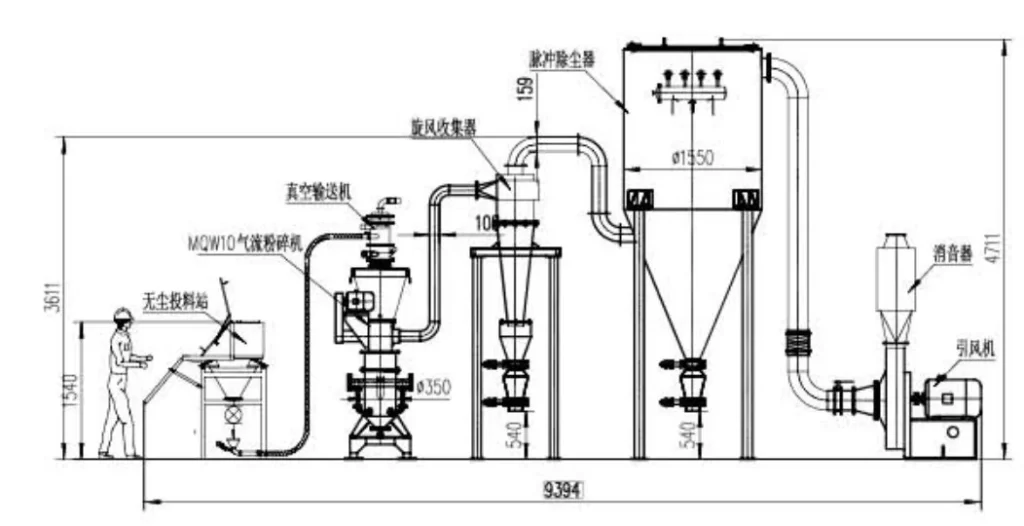
在现代工业生产中,气流粉碎机扮演着至关重要的角色。随着科技的不断进步和各行业对原材料精细度要求的日益提高,气流粉碎机以其独特的优势在众多领域得到了广泛应用。无论是医药、食品、化工还是新材料等行业,对原材料的超微粉碎需求不断增长,而气流粉碎机正是满足这种需求的关键设备之一。
气流粉碎机能够将物料粉碎至微米级甚至亚微米级,为各行业提供高质量的超细粉末。其在医药行业中,可用于制备药物原料的细粉,最大限度地保留药物的活性成分;在食品行业,能改善食品的口感和品质;在化工和新材料行业,满足对原料细度和纯度的严格要求。
正因如此,探讨影响气流粉碎机粉碎效果的因素具有极其重要的必要性。只有深入了解这些因素,才能更好地优化气流粉碎机的工作参数,提高粉碎效率和产品质量,满足不同行业的特定需求。
二、气流粉碎机工作原理
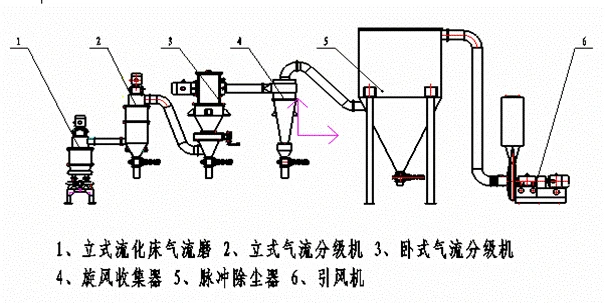
气流粉碎机是一种利用压缩气体将粉体原料吸入粉碎腔,通过喷嘴喷入后使物料颗粒相互碰撞、摩擦与粉碎腔内壁碰撞而粉碎,最终获得超微粉并进入捕集系统的设备。
其工作过程如下:压缩气体(空气或惰性气体)通过加料喷射器的高速射流产生负压,将粉体原料吸入粉碎腔。与粉碎腔半径方向成一定角度并分布在同一平面上的喷嘴,将物料以超高速射流喷入粉碎腔。在粉碎腔内,物料颗粒相互激烈碰撞、摩擦,同时与粉碎腔内壁碰撞,从而实现粉碎。高速射流在粉碎腔内形成强烈的旋流,产生强大离心力,使粉体粒子沿腔壁高速运动。当粉体粒子被粉碎到分级径以下时,受向心气流作用由中心出口进入捕集系统。
例如超微粉气流粉碎机是由气流粉碎机和旋风分离器、除尘器、引风机组成的一整套粉碎系统。首先,把压缩空气经过滤干燥后,通过拉瓦尔喷嘴高速喷射入粉碎腔,经过多股高压气流的喷射之后会形成一个交汇处,物料就在这个高压气流的交汇处被反复碰撞、磨擦、剪切而粉碎。粉碎后的物料在风机抽力作用下随上升气流运动至分级区,在高速旋转的分级涡轮产生的强大离心力作用下,使粗细物料分离,符合粒度要求的细颗粒通过分级轮进入旋风分离器和除尘器进行收集,而不符合粒度要求粗颗粒下降至粉碎区继续粉碎。
气流粉碎机的工作原理决定了它适用领域广、成品细度高、分级精度高等特点。与空气压缩机、冷干机、旋风收集器、除尘器、引风机、控制柜等组成一整套完整的气流粉碎系统,可以广泛的应用于非金属矿、医药食品、陶瓷、环保、新能源、电池材料等众多行业。
三、影响气流粉碎机粉碎效果的因素
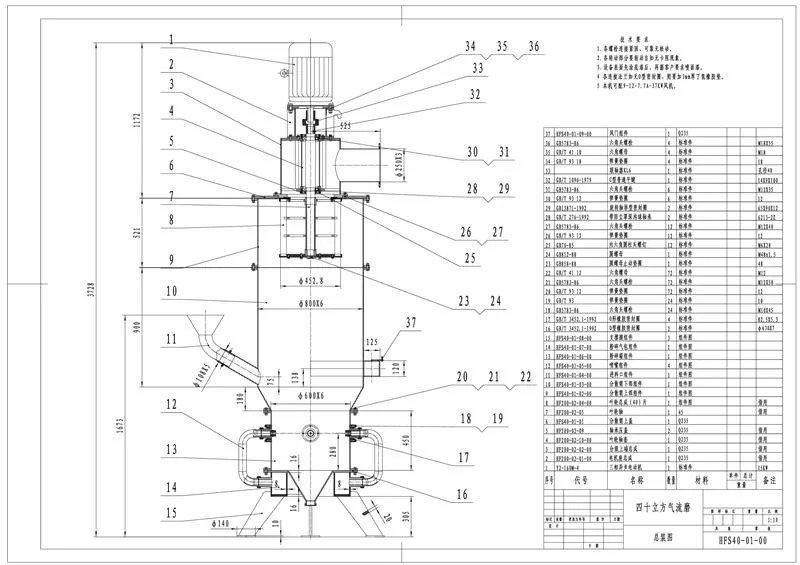
(一)粉碎腔设计的几何参数
粉碎腔直径粉碎腔的直径大小直接决定了粉碎腔的容量。较大直径的粉碎腔能够容纳更多的物料进行粉碎操作,为物料的粉碎提供更广阔的空间。
不同直径下固体进料速率和气体体积流量有着特定的数据关系。例如,研磨腔直径为 50mm 时,固体进料速率为 0.02 – 0.50kg/h,气体体积流量为 0.28 – 0.45Nm³/h;直径为 100mm 时,固体进料速率为 0.10 – 1.00kg/h,气体体积流量为 0.76 – 1.21Nm³/h;直径为 200mm 时,固体进料速率为 1.00 – 7.00kg/h,气体体积流量为 1.80 – 2.70Nm³/h。由此可见,随着粉碎腔直径的增大,固体进料速率和气体体积流量也相应增加。
粉碎腔形状
目前资料暂未详细提及不同形状的粉碎腔对粉碎效果的具体影响,有待进一步的研究和实践来补充这方面的内容。
喷嘴角度
由于喷嘴的存在,粉碎腔内可以分为粉碎区域和分级区域两部分。喷嘴的角度显然决定了这两个区域的大小,进而影响产品的粉碎效果。当喷嘴角度发生变化时,气体在粉碎腔中射流的方向也会随之改变。部分学者认为在相交处流动的气体的相对速度决定了传递给颗粒的动能,从而决定了碰撞的强度。Smit 和 Skelton 等人的研究表明,粉碎效果最好时是在较高的进料速率下,在此考虑切线的角度,Smit 的最佳角度等于 58°,而 Skelton 的最佳值在 52° 和 60° 之间。
喷嘴数量
喷嘴数量是气流粉碎机设计的一个重要特征。以青岛优明科的三个型号(MQW03 MQW06 MQW120) 的气流粉碎机为例,考察过 4 个、6 个、8 个的喷嘴粉碎情况。在保持喷嘴总截面积不变,在粉碎压力和进料速率保持不变的前提下,喷嘴数量越多,粉碎的效果越好。这是因为更多的喷嘴能够提供更多的高速射流,使物料在粉碎腔内的碰撞更加频繁和剧烈,从而提高粉碎效率和产品质量。
(二)操作条件
进料速率
进料速率与粉碎腔内气体 – 固体两相分布密切相关。当进料速率较低时,颗粒在粉碎腔内处于不饱和状态,颗粒所获得的初始动能较大,粉碎后的粒径偏细。这是因为在低进料速率下,颗粒之间的碰撞机会相对较少,颗粒主要与粉碎腔内壁发生碰撞,获得较高的动能,从而被粉碎得更细。
而当进料速度较快时,粉碎腔内的颗粒之间的碰撞概率加大。然而,此时碰撞的粒度不如颗粒与器壁直接碰撞,粒径会有上升的趋势。这是因为在高进料速率下,颗粒之间的碰撞变得更加频繁,但碰撞的强度相对较弱,导致粒径不如低进料速率时细。因此,在稳定生产条件下,进料速度的选择直接影响粒径分布的结果。
喂料量
青岛优明科的气流粉碎机采用的是水平式的双螺杆进料器,通过马达转动带动螺杆的运动,从而推送物料进入粉碎腔内。这种进料器的工作原理是利用螺杆的旋转运动,将物料平稳地输送到粉碎腔中,确保进料的稳定性和连续性。
在恒定的转速条件、粉碎压力条件下,通过对不同重量物料进行粉碎处理,可以看到粒径分布的规律:随着喂料量的增大,粒径分布有增长的趋势。这是因为随着喂料量的增加,粉碎腔内的物料浓度增大,颗粒之间的相互作用增强,导致粉碎效果受到一定影响,粒径分布变宽。
粉碎压力
粉碎压力大小是影响喷射气流速度的重要因素。压力越大,喷射气流速度越高。这是因为在气流粉碎机中,压缩气体通过喷嘴喷入粉碎腔,产生高速射流。当粉碎压力增大时,气体的压缩程度增加,喷射速度也随之提高。
被加速的颗粒在粉碎腔内碰撞速度越高,因此粉碎程度越彻底,产品粒度分布越窄。高速碰撞使得颗粒能够更充分地破碎,达到更细的粒度,同时也使得粒度分布更加集中。
进料压力
进料压力通常要高于粉碎压力 0.5bar 到 1.0bar 之间,这是为了避免文丘里管处的物料回流到喂料器中。通过保持一定的压力差,可以确保物料顺利进入粉碎腔,而不会发生逆流现象。
当进料压力过高时,来自文丘里管的气流会扰乱粉碎腔内的螺旋气流,这时会导致粉碎腔出口处的产品粒径较大。过高的进料压力会破坏粉碎腔内的气流稳定性,影响颗粒的碰撞和粉碎过程,从而使产品的粒径变大。
(三)待粉碎的物料
物料结块情况
进行气流粉碎前,待粉碎的物料本身不能有明显的硬结块。这是由于气流粉碎机的物料入口的直径决定的,若物料有硬结块,会发生物料返喷现象,造成收率降低且生产效率不佳。硬结块的物料在进入粉碎腔时,可能会堵塞入口,或者在粉碎过程中无法被充分粉碎,导致物料反流,影响生产的正常进行。
物料性质
水溶性的结晶性物料,在较低的粉碎压力条件下就可以粉碎到 10 微米左右。这是因为这类物料的性质决定了它们在特定的粉碎条件下更容易被粉碎。
物料本身是否容易引起静电吸附也会影响粉碎效果。如果物料容易引起静电吸附,可能导致粉碎腔内物料堆积或者收集管路堵塞,导致无法正常进行粉碎操作。静电吸附会使物料聚集在一起,影响气流的流动和颗粒的碰撞,从而降低粉碎效率。
四、提高气流粉碎机粉碎效果的方法
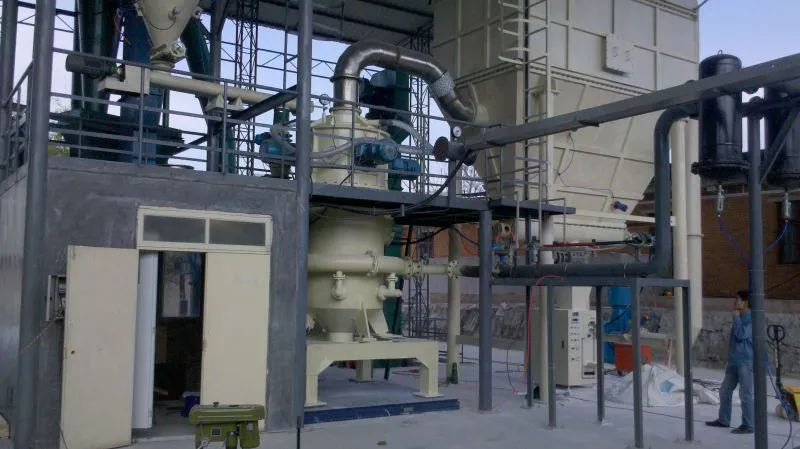
1. 根据不同物料选择合适的粉碎腔设计参数和操作条件。
气流粉碎机的粉碎效果受到多种因素的影响,因此针对不同的物料特性,选择合适的粉碎腔设计参数和操作条件至关重要。
对于不同直径的粉碎腔,应根据物料的处理量和粒度要求进行选择。若物料处理量大且对粒度要求较细,可以选择较大直径的粉碎腔,以提高生产效率和粉碎效果。同时,根据不同的粉碎腔直径,合理调整固体进料速率和气体体积流量,确保物料在粉碎腔内能够充分受到高速射流的作用。
喷嘴角度的选择也应根据物料的特性和进料速率来确定。对于容易粉碎的物料,可以选择接近 Smit 和 Skelton 等人研究的最佳角度范围,以提高粉碎效果。而对于较难粉碎的物料,可以适当调整喷嘴角度,增加气体在粉碎腔内的相对速度,从而提高传递给颗粒的动能,增强碰撞强度。
喷嘴数量的选择则要考虑物料的硬度和粉碎细度要求。对于硬度较高的物料,增加喷嘴数量可以提高粉碎腔内的碰撞频率,使物料更易被粉碎。对于要求高细度的物料,更多的喷嘴能够提供更均匀的射流,使粉碎效果更加理想。
在操作条件方面,根据物料的性质和粒度要求调整进料速率、喂料量、粉碎压力和进料压力。对于容易粉碎的物料,可以适当提高进料速率和喂料量,以提高生产效率。而对于较难粉碎的物料,则应降低进料速率和喂料量,确保颗粒能够获得足够的动能进行充分粉碎。同时,根据物料的硬度和粒度要求调整粉碎压力和进料压力,以获得最佳的粉碎效果。
2. 对物料进行预处理,避免硬结块和静电吸附。
在进行气流粉碎前,对物料进行预处理可以有效提高粉碎效果。对于可能存在硬结块的物料,可以采用防止结块的预处理干燥设备进行处理。例如,使用带有搅拌电机的干燥设备,通过搅拌杆带动搅拌框架转动,利用金属格栅和破碎刀片对物料进行拍打击碎和破碎大块物料,防止物料在干燥过程中凝结成块。此外,还可以采用一种防粉体抱团结块的预处理设备,如气力输送管,通过含粉体的气流进入粗管段和细管段,受到自身和交替压力的作用,使可能结块的粉体结块,再通过筛分将结块物料分离去除,减少后续转运或储存过程中粉体结块的可能性。
对于容易引起静电吸附的物料,可以采取静电防护措施。如使用静电屏蔽材料对设备进行包裹或覆盖,减少静电场的影响。同时,将可能产生静电的设备和金属部件进行接地处理,确保静电能够及时导入大地。在物料方面,可以选择适合的抗静电剂,降低物料的表面电阻率,减少静电荷的产生和积累。在物料输送、搅拌等过程中,适当降低物料的运动速度,避免物料产生剧烈的摩擦、碰撞和分离,减少静电荷的产生。操作人员应穿戴防静电服装和鞋子,避免人体静电对物料的影响。
3. 定期维护和检查气流粉碎机,确保设备正常运行。
为了确保气流粉碎机的粉碎效果,需要定期对设备进行维护和检查。
首先,要检查设备的接地情况,确保所有设备都通过低阻抗接地路径与大地相连,以消除静电电荷积累。同时,采用金属屏蔽罩或导电涂层对设备进行屏蔽,防止外部静电场对设备内部造成影响。定期对接地电阻进行检测,确保其阻值在允许范围内,保证接地效果。
其次,要定期检查设备的易损部件,如喷嘴、分级轮等。对于磨损的部件要及时更换,以确保设备的粉碎效率和产品质量。例如,喷嘴磨损后会导致气流发生偏斜,影响粉碎效率,应及时更换合适的喷嘴。分级轮磨损后,生产率会下降,粒度变粗,发现磨损后应立即更换。
此外,要定期检查设备的传动部件,如电机、皮带、轴承和传动装置等。检查电机的润滑情况,确保电机正常运行。检查皮带的松紧度,确保皮带的工作寿命。检查轴承的温升,当温升超过 50℃时,应停机检查原因并排除故障。
还要定期检查设备的压缩空气管路是否漏气,排放油水分离三联件中积水。检查卸料门是否漏料、密封条是否破损、关门时卸料连杆机构是否处于死点位置。检查压力气管、调节阀和接插件是否松动,有无泄漏。检查压力表反应是否灵敏,有无滞后或者不反应。
最后,在设备长时间不用时,应将腔体内物料清理干净,防止物料堆积影响设备的下次使用。卸料阀和进料机内的润滑油应定期更换,确保设备的正常运转。
五、结论
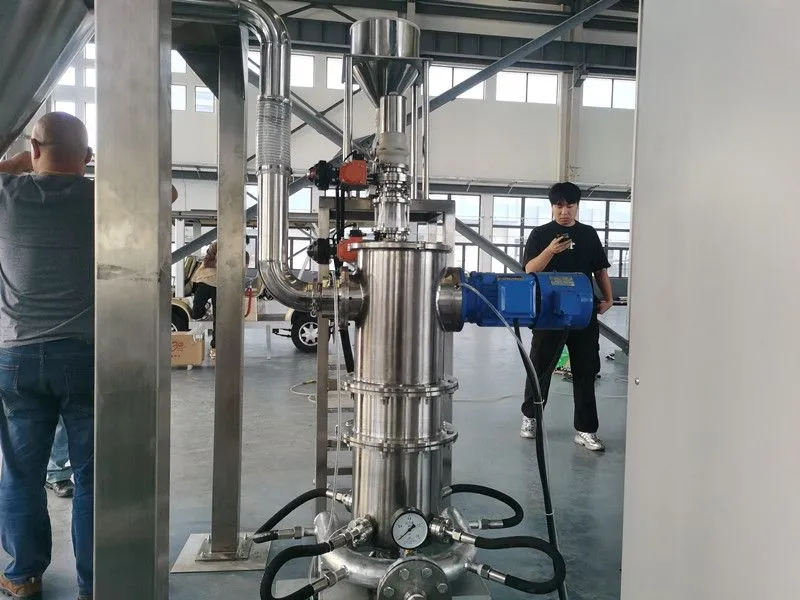
综上所述,影响气流粉碎机粉碎效果的因素众多,了解并合理选择和调整这些因素对于提高粉碎效果至关重要。
首先,粉碎腔设计的几何参数方面,粉碎腔直径直接决定容量,不同直径对应不同的固体进料速率和气体体积流量。喷嘴角度影响粉碎区域和分级区域大小,以及气体相对速度和颗粒动能,合适的角度能提高粉碎效果。喷嘴数量越多,粉碎效果越好。然而,目前对粉碎腔形状的研究尚不充分,有待进一步探索。
其次,操作条件对粉碎效果也有显著影响。进料速率的高低决定了颗粒在粉碎腔内的状态和碰撞情况,进而影响粒径分布。喂料量增大,粒径分布有增长趋势。粉碎压力越大,喷射气流速度越高,粉碎程度越彻底,产品粒度分布越窄。进料压力需高于粉碎压力一定范围,以避免物料回流,但过高的进料压力会扰乱螺旋气流,导致产品粒径变大。
再者,待粉碎的物料自身特性也不容忽视。不能有明显硬结块,否则会发生物料返喷,降低收率和生产效率。水溶性结晶性物料在较低粉碎压力下易粉碎,而容易引起静电吸附的物料可能导致粉碎腔内物料堆积或收集管路堵塞。
为提高气流粉碎机的粉碎效果,可以根据不同物料选择合适的粉碎腔设计参数和操作条件。针对不同特性的物料,合理调整粉碎腔直径、喷嘴角度和数量、进料速率、喂料量、粉碎压力和进料压力等参数。同时,对物料进行预处理,避免硬结块和静电吸附,如采用防止结块的预处理干燥设备和静电防护措施。此外,定期维护和检查气流粉碎机,确保设备正常运行,包括检查接地情况、易损部件、传动部件、压缩空气管路等,及时清理设备内物料和更换润滑油。
总之,通过综合考虑和优化这些影响因素,能够充分发挥气流粉碎机的优势,提高粉碎效率和产品质量,满足各行业对超微粉碎的需求。